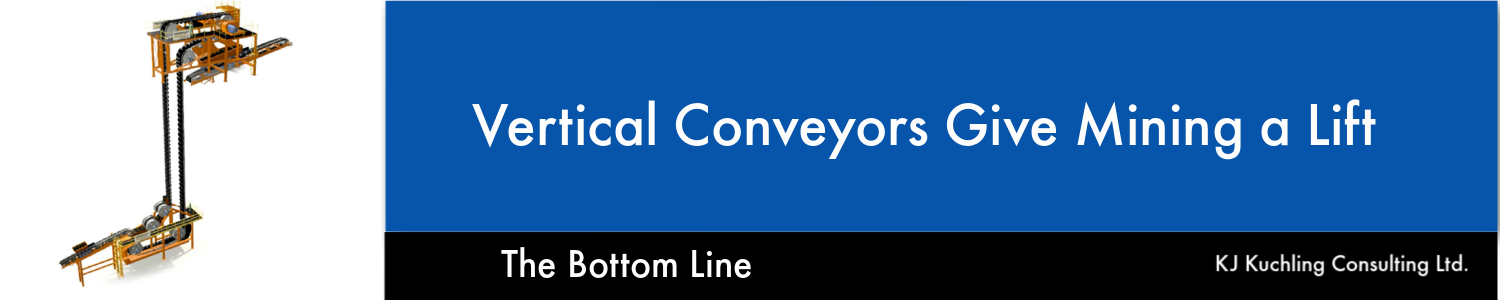
There are not many things that are novel to me after having worked in the mining industry for almost 40 years. However recently I came across a mining technology that I had heard very little about. It’s actually not something new, but it has never been mentioned as a materials handling option on any project that I am aware of.
That innovative technology is vertical conveying. Not long ago I read about a vertical conveyor being used at the Fresnillo underground mine, hoisting 200 tph up from a depth of 400 metres and had a capital cost of $12.7 million.
I was aware of steep angle conveyors being used in process plants. However they tended to be of limited height and have idlers and hardware along their entire length. Vertical conveyors are different from that.
After doing a bit of research, I discovered that vertical conveyors have been used since the 1970’s. Their application was mainly in civil projects; for example in subway construction where one must elevate rock from the excavation level up to street level. The mining industry is taking vertical conveyors to the next level.
I have never personally worked with vertical conveyors. Therefore I am providing this discussion based on vendor information. My goal is to create awareness to readers so that they might consider its application for their own projects.
How vertical conveying works
The background information on vertical conveying was provided to me by FKC-Lake Shore, a construction contractor that installs these systems. FKC itself does not fabricate the conveyor hardware. A link to their website is here.
The head station and tail station assemblies are installed at the top and bottom of a shaft. The conveyor belt simply hangs in the shaft between these two points. There is no need for internal guides or hardware down the shaft. The conveyor belting relies on embedded steel cables for tensile strength and pockets (or cells) to carry the material.
The Pocketlift conveyor system is based on the Flexowell technology. This has been advanced for deep underground applications with a theoretical lift height of 700 metres in one stage. The power transfer is achieved by two steel cord belts that are connected with rigid cross bars. The ore is fed into rubber pockets, which are bolted onto the cross bars. The standard Pocketlift can reaches capacities up to 1,500 m3/h and lift heights up to 700 m, while new generations of the technology may achieve capacities up to 4,000 m3/h.
The FLEXOWELL®-conveyor system is capable of running both horizontally and vertically, or any angle in between. These conveyors consist of FLEXOWELL®-conveyor belts comprised of 3 components: (i) Cross-rigid belt with steel cord reinforcement; (ii) Corrugated rubber sidewalls; (iii) transverse cleats to prevent material from sliding backwards. They can handle lump sizes varying from powdery material up to 400 mm (16 inch). Material can be raised over 500 metres with reported capacities up to 6,000 tph.
The benefits of vertical conveying
Vendors have evaluated the use of vertical conveying against the use of a conventional vertical shaft hoisting. They report the economic benefits for vertical conveying will be in both capital and operating costs.
Reduced initial capital cost due to:
-
Smaller shaft excavation diameter,
-
Reduced cost of structural supports vs a typical shaft headframe,
-
Structural supports are necessary only in the loading and unloading zones and no support structures in the shaft itself since the belt hangs free.
Lower operating costs due to:
-
Significantly reduced power consumption and peak power demand,
-
Lower overall maintenance costs,
-
No shaft inspections required,
-
The belt is replaced every 8 – 10 years.
Conclusion
We chose this option for a mine, as it saved us about 50m of shaft depth. You don’t need the shaft bottom arrangements and extra space you would have for skips and trailing cables. You therefore save some serious capex there. Also several months on critical path of implementation schedule. Shaft steel work is also simplified significantly, improving schedule further.
Hi Paul, thanks for the feedback. Hopefully others take a look at it too.
Ken