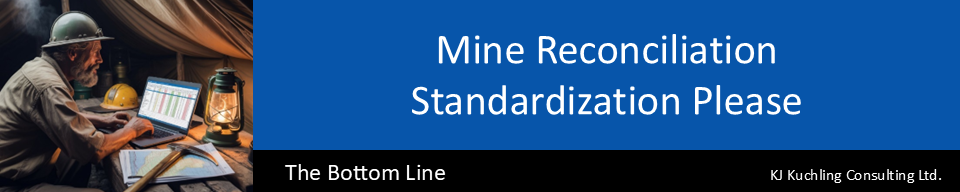
Mine through mill reconciliation, in my view, is an under appreciated topic that could benefit from more conversation amongst industry members. Unfortunately, reconciliation is sometimes viewed as a time consuming frustrating activity, with what some consider less than verifiable results. However given the ongoing innovation that we are seeing in mining, reconciliation may need to play a bigger role than ever.
The mining industry is implementing more and more technology in the mining cycle.
For example, this can range from AI assisted resource modelling, down hole logging, blast movement tracking, GPS controlled dig limits, MineSense bucket grade tracking, load scanning, truck dispatch control, smart mining and edge computing, online grade analyzers, belt weightometers, drone surveying of stockpiles, and real time process controls.
Lots of different innovations are continually being adopted by the mining industry, contrary to what some may say.
The question is does all this innovation improve the overall performance of a mining operation, and if so, by how much? It can cost a lot of money to implement the new technology, is there a payoff?
One cannot answer those questions if one doesn’t undertake proper mine reconciliation. A concern might be that mining is innovating faster than the ability to assess the results of that innovation. To monitor it, you need to measure it.
What is Mine Reconciliation
Mine reconciliation is the process of comparing and aligning the estimated production with the actual production from mining and processing. It requires assessing the accuracy of pre-mining predictions against actual results to identify inconsistencies in the system and hopefully improve it, be it resource estimation, mine planning, or process efficiency. Comparisons can be made between multiple stages in the mining system, as shown in the image below.
-
Mine reconciliation requires information such as initial predictions from exploration data and geological models, actual measurement: data from mining sources, such as blast holes, stockpile samples, or mill feed. As well it will need data on the final product being shipped off site. Do the metal quantities balance out throughout the mining operation?
-
Mine reconciliation tends to aggregate over longer time periods (monthly, quarterly or annually) due to short term impacts of material handling in stockpiles and plant circuits and the labour time needed to collect the input data.
-
Mine reconciliation ultimately attempts to assess how well the delivery of the final metal product relates to the initial resource model (i.e. what the project decision was originally based on)? It is also tool to evaluate the impact of any innovation implementation on the operation.
-
Reconciliation will help mine operators highlight issues and optimize extraction, manage costs, and ensure compliance with regulatory or investor expectations. Factors such as poor resource estimation, excessive dilution and ore loss, inaccurate sampling, etc. can cause discrepancies, making reconciliation an important part of any operation.
-
The reconciliation process is also used to derive Mine Call Factors. These factors are used to modify the forecasts from long range models, short range models, and grade control models to better represent the actual performance the operation will likely see. Large call factors suggest something is amiss in the “forecast to actual” progression. The first problem is to identify the causes. The list of the common sources of error can be lengthy. Then, once identified, the second problem is how to fix them.
Harry Parker initially suggested various reconciliation parametrics and labelled them F1, F2, F3. In a 2009 paper by Fouet titled “Standardising the Reconciliation Factors Required in Governance Reporting”, indicates that Rio Tinto had decided upon fifteen (15) different possible reconciliation correlations (see image below). Each one provides an insight on the efficiency of the operation in one way or another. I have seen modified versions of the reconciliation relationships, so it appears there may be no industry standard at this time. Fouet was asking about industry standardization in 2009 (an excellent paper to read by the way).
Mining Codes Getting Involved
It appears that the JORC Code may be recognizing the importance of reconciliation. In an August 2024 Exposure Draft JORC is suggesting the following text: “Where an Ore Reserve has been publicly reported for an operating mine, the results of both production reconciliation and any prior estimate comparison must also be included in the annual Mineral Resources and Ore Reserves statement. Refer to Clause 2.36. The relationships and variables being reconciled must be described in plain language or depicted graphically and must include reconciliations of both the Mineral Resources and Ore Reserves.”
Interestingly, it appears that NI43-101 has not yet jumped on the bandwagon about the importance of disclosing reconciliation results. However, it may just be a matter of time before it becomes one of their disclosure requirements.
If more regulatory focus will be put on mine reconciliation disclosure, then perhaps more industry standardization is warranted. This would help better define some of the terminology and “F factors” shown in the diagrams above to ensure consistency and help avoid each mine doing reconciliation in their own way.
Excel versus Cloud Based Reconciliation
Each mine site may be unique with respect to; ore sources; terminology; ore types; mining methods; stockpiling philosophy; processing methods; technology availability; and personnel capability. So often the easiest approach for mine reconciliation is based on the Excel spreadsheet. (Reconciliation is generally not an easy undertaking).
Spreadsheets can be built site specific, based on an operation’s unique characteristics.
Spreadsheets are often built by a user for that user. They are tailored for the tailor. In my experience, typically the modeler is the only one comfortable with an Excel model’s logic, since all of us may think differently. Unfortunately, with the spreadsheet approach, it becomes more difficult to standardize an industry wide reconciliation process.
An alternate solution to spreadsheets is to use a cloud based standardized software package. Toronto based Minebright has one option, called Pit Info (see link for more info). There are a few other reconciliation software applications available. They tend to be cloud based, hence multiple people can have access to the input modules or output modules. (I would like to thank the Minebright people for steering me towards some of the technical papers on this subject).
The cloud based approach may help make reconciliation a group effort instead of a tightly controlled internal function. It may also help standardize reporting from a company’s multiple operations, reporting from the mining industry globally, or simply for consistent JORC reporting.
The downside to the cloud approach is the mine site teams must learn the software and tailor it to their operation. However, once that hurdle is passed, personnel changes become less onerous due to the model consistency. I have seen cases where a person doing the Excel reconciliation task has left their job, and hence forward the reconciliation effort came to a halt. The people remaining may be too busy or simply don’t want to have to figure out the Excel logic of someone else.
The other nice thing about a cloud software approach is that when improvements are rolled out, every user gets the same update. The “wisdom of crowds” will result in learnings and suggestions that will tend to improve the application functionality over time. There are a lot of smart people out there, and it would be nice to see them working together rather than individually, as the open source software community has demonstrated.
With AI, we also may get to the point where cloud based mine reconciliation platforms can use learnings from other projects, and help identify where the likely technical shortfalls are at a mine site and why production is not reconciling. Let’s ask AI do some of the thinking for us to get to the bottom of a problem.
Conclusion