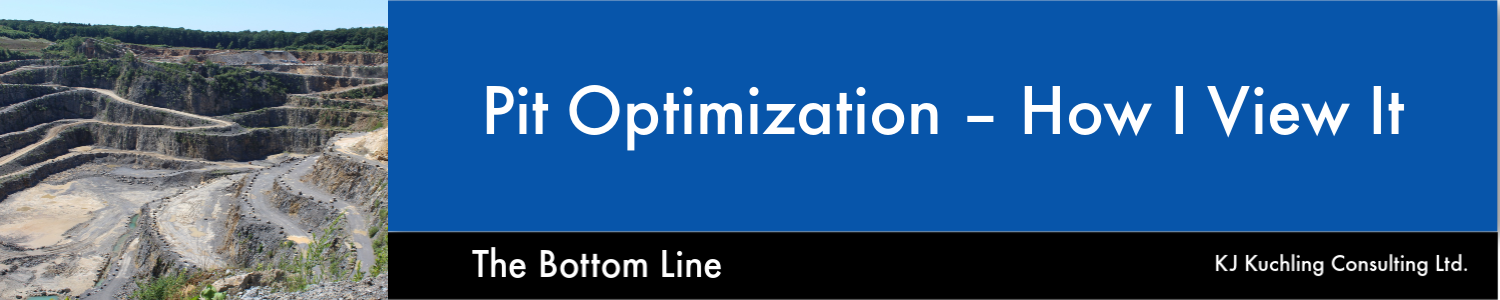
One of the first steps in an open pit design is the pit optimization analysis. Pit optimization is used to define the most profitable pit shell for a given set of economic parameters. The economic parameters include the metal prices, processing recoveries, and site operating costs. Normally when optimization is done, a range of metal prices or Revenue Factors (“RF”) is used to develop a series of nested shells to understand how the pit will expand or contract with increasing or decreasing metal prices.
Once the optimization step is complete, mining engineers will then design the pit inside that shell, introducing benches and ramps. The pit design should mimic the selected optimized shell as closely as possible.
The pit design may (or may not) closely replicate the optimization shell depending on the slope angles used in the optimization and where the haul ramps are located in the design.
Hence the actual ore and waste tonnages mined may be different that the tonnages defined by the optimizer.
Various experts in pit optimization will use approaches of differing complexity. Some may apply variable mining costs with pit depth; apply variable process recoveries linked to head grade; apply variable pit slopes by sector or depth, apply dilution and ore losses; etc. One can make the pit optimization step as simple or detailed as one wants it.
The question is whether detailed pit optimization is warranted. My view is that overly detailed pit optimization is not required, other than if one wants to test parameter sensitivity on the resulting pit size and shape. There are just too many uncertainties in the parameters being used in optimization.
Open Pit Optimization Uncertainties
Some of the uncertainties involved in the optimization approach are listed below:
-
Pit optimization can generate large pits that would have a long mine life. However one doesn’t really know the metal prices far into the future. So will that final pit ever get mined, or might it even be larger than shown.
-
Pit optimization is typically done at the start of a study, so one doesn’t have the detailed operating costs yet. The size of the project may be unknown and one has to use rough estimates for future costs and possibly even assume preliminary process recoveries.
-
Operating costs will also change in the future, and the optimization step is just a snapshot using current information.
-
Sometimes the optimization includes the use of Inferred resources, which are uncertainty. Sometimes optimization is done only using Measured and Indicated resource, yet there may be areas if Inferred resource that ultimately convert to M &I and these will have been ignored. So, either way you do it, you are not sure what ore the pit can captured and will to shape the pit.
-
The smaller pits, if developed, would consist of smaller operations and may have different operating costs than assumed in the optimization. Similarly larger pits may have different throughput rates and operating costs than assumed in the optimization.
-
The ore and waste split reported within the pit will be based on a specific life-of-mine cutoff grade. This is based on the fixed metal price and operating cost assumptions applied.
-
Overall pit wall slopes may differ for shallow pits versus deep pits. Slopes may vary above the groundwater table and below it. In many instances during pit optimization the wall angles are maintained at the same angle irrespective of the pit depths. Sometimes geotechnical programs have not yet been completed, so optimization slope angles are simply educated guesses.
-
Dilution may be applied globally during pit optimization (unless one is working with a diluted block model). In reality, dilution may differ in different parts of the ore body, and that may not be considered in the optimization stage. For more discussion on dilution in general, read the blog “Ore Dilution Prediction – Its Always an Issue“.
Conclusion
I agree wholeheartedly with your bottom line but would point out one additional necessary factor, which is a discount rate. Without it you won’t see much in terms of optimal cash flow.
Over time I’ve come to realize that revenue trumps cost by a factor of about 2 to 1, so improving grade or recovery will have more impact on pit size than decreasing waste.
It’s also important to note that pit optimization uses the resource model to develop pit shells, and the accuracy of the resource model must be defined before one spends a lot of time on varying bench costs or other bells and whistles. The ultimate shell will not be more precise than the model allows.
I agree that the resource model is another issue to consider in optimization. If your resource model has a significant proportion of inferred ore, particularly towards the base of the block model where the pit bottom is being optimized, then there is another level of uncertainty. For a PFS or FS, inferred ore is ignored but any uncertainty in the model itself is still a factor in deciding how accurate the optimization result really is.
I don’t ignore inferred when developing the pit shell but I don’t include it when calculating the reserve.
That’s an interesting approach. I don’t recall seeing any PFS or FS where inferred was included in the optimization but then not included when reporting the reserve inside the pit. Usually the inferred is just flagged as waste for both optimization and reporting. Your approach does have merit. At a minimum one should run the optimization with and without inferred to see the impact that it has.
It’s more common in Oz. If you have time, check out Altona. (ASX) Their DFS included work done by a group called Optiro. That’s how they did it.
Hardrockminer, that is incorrect.
Under JORC 2012, you cannot include Inferred in any optimisation work when declaring Reserves.
If you are, then you should be taken out the back and shot.
So that is not “how we do things in Oz”!!
Rather than using Optiro, maybe you should be using SRK or CSA Global.