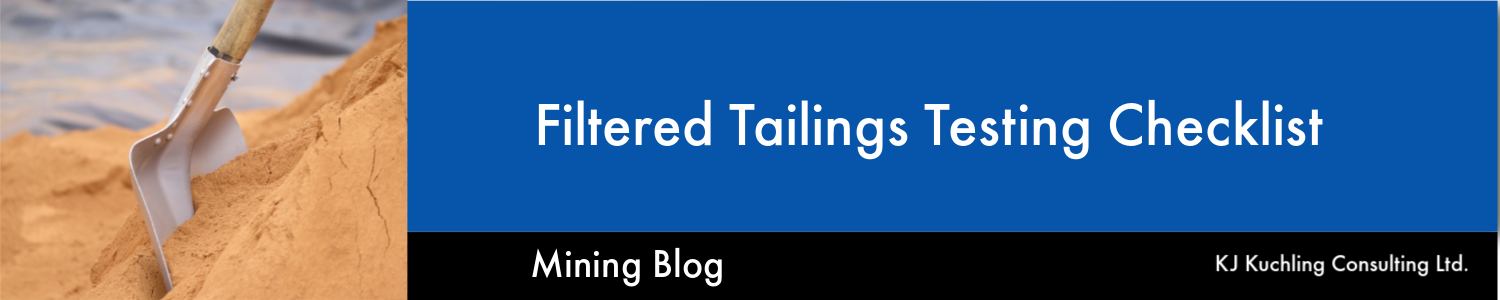
I have always been a big proponent of filtered (or dry stack) tailings over conventional tailings disposal. Several years ago I had written a blog (Fluid Tailings – Time to Kick The Habit?) that this is the tailings disposal approach the mining industry should be moving toward.
Recently I have been seeing more mining studies proposing to use the dry stack approach. In some cases, they no longer even do the typical tailings trade-off study that look at different options. The decision is made upfront that dry stack is the preferred route due to its environmental acceptability and positive perceptions.
Recently I came across a nice document prepared by BHP and Rio Tinto titled “Filtered Stacked Tailings – A Guide for Study Managers (March 2024)”. I will refer to this document as “The Guide”. You should definitely get a copy of this Guide if your project is considering a dry stack operation. An information link is included at the end of this post.
A Guide for Study Managers
The Guide covers several topics, including tailings characterization; site closure concepts; filtered tailings stack design; material transport, stacking systems; and tailings dewatering methods. The Guide covers all the basics very well. The one area that jumped out at me is the tailings characterization and testing aspect.
Many assume that dry stack is simply filter, haul, dump, then walkaway. Its all very easy! However, in reality, the entire dry stack approach is complex.
One needs to be able to consistently dewater tailings from different ore types, then transport it under different climatic conditions, and then place and compact the tailings efficiently.
One also needs to be able to deal with plant upsets, when the filtered tailings don’t meet the optimal product specifications. So its not really that simple.
One of the chapters in the Guide details the different test work that should be done to understand the dry stack approach. The list of tests is a lot longer than I had envisioned. I previously knew some of the types of lab testing required, however the Guide outlines a very comprehensive list.
The Guide also categorizes the tests according to study stage, be it concept study, order of magnitude study, or Pre-Feasibility level. Interestingly, the concept study can rely mainly on published information. However, the more advanced mining studies require the lab testing of actual tailings material.
Testing Checklist
To help organize the complexity of testing, I have listed their suggested tests as to whether the test is related to material characterization, process characterization, or filtered product characterization. Each aspect serves a different purpose in understanding the workings of the filtered tailings approach. The engineer will decide at which study stage they wish to do each of the tests, or which of the them they actually need to do.
To keep the blog post brief, I am not describing the details for each test. Most geotechnical or process engineers will already be familiar with them, or anyone can search the web to learn more.
MATERIAL CHARACTERIZATION TESTS
-
Chemical composition Testing: using atomic absorption or spectroscopy, identify the elements within the tailings stream to highlight contaminants and potential flocculation issues.
-
Conductivity Test: increase knowledge of the tailings stream.
-
Mineralogy Testing: identify mineral types and clay minerals (if any) that could impact on performance.
-
Particle Shape Analysis: are there fibrous minerals present, as well as settling and rheology effects.
-
Particle Size Distribution: are the tailings coarse, or mainly fine silt and clay sized particles that can impact on filtering and product performance.
-
pH Test: determine the acidity of the tailings steam, can relate to flocculant selection.
-
Tailings Slurry Density Test: assess the pumpability and amount of thickening and filtering that will be required.
-
Tailings Solid Mass Concentration and Moisture content: required for process mass balances.
-
Specific Gravity Testing: assess the SG of the tailing particles, i.e. light or heavy minerals.
-
Total Dissolved Solids Test: assess the fluid composition, are minerals dissolvable.
-
Zero Free Water Test: relates to the solids concentration at which the sample is fully saturated and may relate to transportability.
PROCESS CHARACTERIZATION TESTS
-
Total Suspended Solids: assess the quality of the return water from thickening or filtration.
-
Drained and Undrained Settling Test: to assess the thickening aspects and stack performance.
-
Setting Cylinder Tests: used to assess thickener settling performance.
-
Raked Setting Cylinder Tests: used to assess thickener settling performance.
-
Dynamic Continuous Settling Tests: used to assess thickening under continuous feed situation.
-
Minimum Moisture Content: assess the minimum moisture content achievable in filtration.
-
Vacuum/Pressure Filtration Test: often done by vendors, assess the filtering performance.
-
Compression Rheology: design consolidation / permeability data for filtering and disposal design.
-
Shear Rheology: provide information for pump and pipeline design.
-
Shear Yield Stress: provide processing insights for slurry dispersion and flocculation.
FILTERED PRODUCT CHARACTERIZATION TESTS
-
Leaching Tests (long term): assess whether the tailings stack will continue to leach metals and contaminants over the long term.
-
Leaching Tests (short term): assess whether the tailings stack will rapidly leach metals and contaminants.
-
Acid Base Accounting Tests: will the stack be an ARD concern.
-
Net Acid Generation: relates to ARD and neutralizing potential.
-
Air Drying Tests: determine the rate of natural air drying and dry density.
-
Atterberg Limits Testing: determine the plastic limit, liquid limit with respect to moisture content and stackability.
-
Consolidation Tests (one-dimensional): to assess the consolidation and settlement of the stack over time.
-
Proctor Density Tests: assess the optimal compacted density and moisture content vs the moisture content delivered by filtration.
-
Critical Void Ratio Tests: assess compaction, consolidation, and liquefaction potential.
-
Shear Testing: determine the geotechnical strength of the filtered product for stack height design.
-
Permeability Testing: assess the internal drainage characteristics of the filtered product.
-
Soil-water characteristics Tests: assess the unsaturated behavior of the filtered product.
-
Flow Moisture Point Tests: assess how well the material can be transported and placed.
-
Conveyance Testing: assess how well the material can be conveyed (troughing, steepness).
-
Minimum Angle for Discharge: used in the design of hoppers and chutes.
-
Angle of Repose Tests: used in hopper design and dry stack design. Ground Bearing Pressure: used to assess the trafficability of the deposit.
Conclusion
A dry stack operation might be just as complex as conventional tailings disposal, although that might not be the perception. Certainly, the processing side of filtered tailings is more complex than conventional tailings. The transportation design may also be more complex, as is the tailings placement methodology. The main complexity missing from the dry stack is the need for a large sludge retaining dam, albeit that is a huge and important difference.
Some might view the suggested testing checklist as overkill and decide that not all test work is necessary. That is most likely true for some situations, especially for small mines not dealing with large quantities of tailings. However for a project with a high capital investment, one doesn’t want to see the entire mill off-line because the tailings disposal system isn’t functioning.
Major miners, such as BHP and Rio Tinto, typically spare no expense on material testing for metallurgical or geotechnical purposes. They have the funds available to test and engineer to a high level to adequately de-risk the project to meet their investment thresholds.
Junior miners often don’t have the time or funds to spend on such comprehensive testing programs. “Good enough” is often good enough.
One reason why junior miners sign 5-year JV deals with the Major is the amount of technical work required to properly evaluate a project.
The Major understands the amount of time needed for sample collection, testing, analysis of results, and follow up with more testing. It takes a fair bit of time to reach a comfort level for moving forward. Even then, there are no guarantees of success.
Each tailings disposal project is unique in size, location, type of mineralization, site layout, and throughput rate, so each company must decide what level of testing is “good enough” to address their risk tolerance.
For those that would like to get a copy of the the Guide, you can find more information at this LinkedIn link. I thank BHP and Rio Tinto for putting their heads (and wallets) together to prepare (and share) this document.