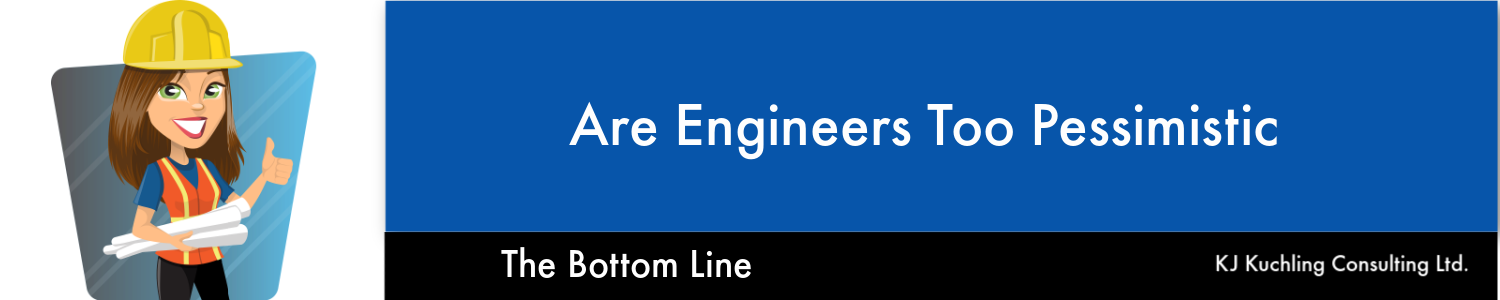
Geological colleagues have often joked that engineers are a pessimistic lot; they are never technically satisfied. The engineers will fire back that geologists are an overly optimistic lot; every speck of mineralization makes them ecstatic. Together they make a great team since each cancels the other out.
In my opinion engineers are often pessimistic. This is mainly because they have been trained to be that way. Throughout my own engineering career I have been called upon many times to focus on the downsides, i.e. what can happen that we don’t want to happen.
It starts early and continues on
This pessimism training started early in my career while working as a geotechnical engineer. Geotechnical engineers were always looking at failure modes and the potential causes of failure when assessing factors of safety.
Slope failure could be due to the water table, excess pore pressures, seismic or blast vibrations, liquefaction, unknown weak layers, overly steepen slopes, or operating error. As part of our job we had to come up with our list of negatives and consider them all. The more pessimistic view you had, the better job you did.
This training continued through the other stages of a career. The focus on negatives continues in mine planning and costing.
For example, there are 8,760 hours in a year, but how many productive hours will each piece of equipment provide? There will delays due to weather conditions, planned maintenance, unplanned breakdowns, inter-equipment delays, operator efficiency, and other unforeseen events. The more pessimistic a view of equipment productivity, the larger the required fleet. Geotechnical engineers would call this the factor of safety.
In the more recent past, I have been involved in numerous due diligences. Some of these were done for major mining companies looking at acquisitions. Others were on behalf of JV partners, project financiers, and juniors looking at acquisitions.
When undertaking a due diligence, particularly for a major company or financier, we are not hired to tell them how great the project is. We are hired to look for fatal flaws, identify poorly based design assumptions or errors and omissions in the technical work. We are mainly looking for negatives or red flags.
Often we get asked to participate in a Risk Analysis or SWOT analysis (Strengths-Weaknesses-Opportunities-Threats) where we are tasked with identifying strengths and weaknesses in a project.
Typically at the end of these SWOT exercises, one will see many pages of project risks with few pages of opportunities.
The opportunities will usually consist of the following cliches (feel free to use them in your own risk session); metal prices may be higher than predicted; operating costs will be lower than estimated; dilution will be better than estimated; and grind size optimization will improve process recoveries.
The project’s risk list will be long and have a broad range. The longer the list of risks, the smarter the review team appears to be.
Investing isn’t easy
After decades of the training described above, it becomes a challenge for me to invest in junior miners. My skewed view of projects carries over into my investing approach, whereby I tend to see the negatives in a project fairly quickly. These may consist of overly optimistic design assumptions or key technical aspects not understood in sufficient depth.
Most 43-101 technical reports provide a lot of technical detail; however some of them will still leave me wanting more. Most times some red flags will appear when first reviewing these reports. Some of the red flags may be relatively inconsequential or can be mitigated. However the fact that they exist can create concern. I don’t know if management knows they exists or knows how they can mitigate them.
It has been my experience that digging in a data room or speaking with the engineering consultants can reveal issues not identifiable in a 43-101 report. Possibly some of these issues were mentioned or glossed over in the report, but you won’t understand the full extent of the issues until digging deeper.
43-101 reports generally tell you what was done, but not why it was done. The fact I cannot dig into the data room or speak with the technical experts is what has me on the fence. What facts might I be missing?
Statistics show that few deposits or advanced projects become real mines. However every advanced study will say that this will be an operating mine. Many projects have positive feasibility studies but these studies are still sitting on the shelf. Is the project owner a tough bargainer or do potential acquirers / financiers see something from their due diligence review that we are not aware of? You don’t get to see these third party reviews unless you have access to the data room.
My hesitance in investing in some companies unfortunately can be penalizing. I may end up sitting on the sidelines while watching the rising stock price. Junior mining investors tend to be a positive bunch, when combined with good promotion can result in investors piling into a stock.
Possibly I would benefit by putting my negatives aside and instead ask whether anyone else sees these negatives. If they don’t, then it might be worth taking a chance, albeit making sure to bail out at the right time.
Often newsletter writers will recommend that you “Do your own due diligence”. Undertaking a deep dive in a company takes time. In addition I’m not sure one can even do a proper due diligence without accessing a data room or the consulting team. In my opinion speaking with the engineering consultants that did the study is the best way to figure things out. That’s one reason why “hostile” due diligences can be difficult, while “friendly” DD’s allow access to a lot more information.
Conclusion
Sometimes studies that I have been involved with have undergone third party due diligence. Most times one can predict ahead of time which issues will be raised in the review. One knows how their engineers are going to think and what they are going to highlight as concerns.
Most times the issue is something we couldn’t fully address given the level of study. We might have been forced to make best guess assumptions to move forward. The review engineers will have their opinions about what assumptions they would have used. Typically the common comment is that our assumption is too optimistic and their assumption would have been more conservative or realistic (in their view).
Ultimately if the roles were reversed and I were reviewing the project I may have had the same comments. After all, the third party reviewers aren’t being hired to say everything is perfect with a project.
The odd time one hears that our assumption was too pessimistic. You usually hear this comment when the reviewing consultant wants to do the next study for the client. They would be a much more optimistic and accommodating team.
To close off this rambling blog, the next time you feel that your engineers are too negative just remember that they are trained to be that way. If you want more positivity, hang out with a geologist (or hire a new grad).