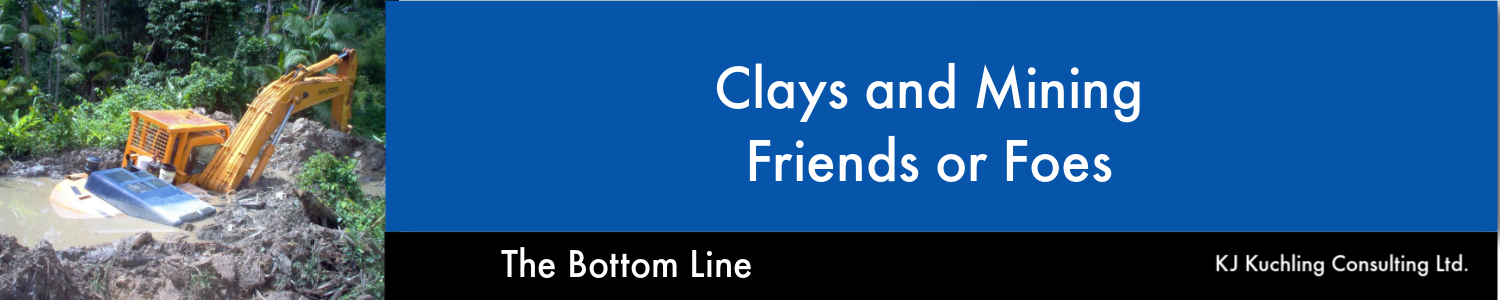
Overburden is a generalized termed used to describe unconsolidated material encountered at a mine. It can consist of gravels, sands, silts, and clays and combinations of each. Usually overburden is not given much focus in many mining studies. Very often, the overburden as a unit, is not adequately characterized.
This blog will explain why proper characterization can be an important issue, particularly the clay component.
I also want to share some personal mining experiences with clays, all types of clays. There is more to them than meets the eye; a fact often not apparent to those involved only in hard rock mining.
Clays have unique geotechnical properties that can make for challenging situations and require special consideration in project design. Many simply view clay as a sticky cohesive material – no big deal. So let’s examine this a bit further. I tried to avoid geotechnical lingo where possible, since this blog isn’t being written for geotechnical engineers.
There are several types of clays, or clay-like materials that can be encountered in mining. Here are the ones that I have been lucky (or unlucky) enough to have dealt with over the years.
-
Normally consolidated clays
-
Over-consolidated clays
-
Sensitive (or quick) clays
-
Swelling clays
-
Saprolite clays
-
Kimberlite clays (muds)
What are the challenges?
Each of the clays listed above can be found in different locations, have unique properties, will behave differently, and can create specific mining challenges. Clays can also cause problems in process plant circuits, but that is a subject outside my area of expertise.
Normally consolidated clays
These are the clays most people are familiar with, i.e. a sedimentary deposit of very fine particles that have settled in a calm body of water. Normally consolidated clays are generally not a problem, other than having a high moisture content. As such, they can be very sticky in loader buckets, truck boxes, and when feeding crushers.
When wet, they can become sloppy and difficult to handle efficiently. They can creep and run when placed into waste dumps. For these reasons, engineers must be aware if a large proportion of the overburden will consist of clays so they can avoid surprises.
Over-consolidated clays
These clays have undergone greater vertical compression in their history than in their current condition. For example, perhaps they were once pre-loaded and compressed by a mile of glacial ice sheet during an ice age, which has subsequently melted.
Clays in general consist of very fine plate like particles, as shown in this sketch. In over-consolidated clays, these particles have been flattened and tightly compressed as in the right image. The result is that the clay may be dense, have a good cross bedding shear strength, but very low shear strength along the plates. This characteristic is analogous to the lubricating properties of graphite, which is facilitated by sliding along graphite plates.
My experience in working with over-consolidated clays was at the Fort McMurray oil sands mining operations. In that region the Clearwater clays formed part of the overburden sequence above the oil sands. Stripping these clays with trucks and shovels was not exceptionally challenging. They had low moisture content and were stiff. The challenge really came when needing to build on top of them, for example building a waste dump or tailings dam.
The cross-bedding shear strength was good, with peak friction angles exceeding 25 degrees. However after any creep or deformation, the peak shear strength was gone and the residual friction angle would now control stability. The residual friction angles could drop as low as 6 degrees (very weak) and, upon surcharging the clay could maintain high internal pore pressures. Due to these factors it was not uncommon to see tailings dams or waste dumps with 15:1 (H:V) downstream slopes. This compares to the 3:1 slopes one may normally see at hard rock mine sites.
Building a 15:1 dam or dump is much less volume efficient than building a 3:1 embankment. It also doesn’t take much instability to cause an embankment to creep along a foundation with only a 6-degree friction angle. Hence the over-consolidated clays presented a unique engineering challenge when working in the oil sands.
Sensitive (quick) clays
Referring to the clay particle sketch shown above, quick clays represent a card house structure (on the left image). These clays were often deposited in a quiet marine environment, where electrical charges prevented the clays from settling uniformly. Instead, the clay particles tend to stack up like a house of cards. The large void spaces are filled with water, whereby moisture contents can exceed 100% by weight.
When these clays are disturbed by vibration or movement, the house of cards structure collapses. Combined with the excess void water, these clays will flow…. and flow a lot. This video shows a slope failure in quick clays in Norway. Try to stop that failure once it has initiated.
My experience with sensitive clays was at the former BHP bauxite mining operations along the northern coast of Suriname. There were Demerara clay channels up to 20m thick over top of many of their open pits. The bucketwheel excavators used for waste stripping would trigger the quick clay slope failures, sometimes resulting in the crawler tracks being buried and unfortunately also causing some worker fatalities.
I recall walking up towards a bucketwheel digging face as the machine quietly churned away. About 70 metres from the machine, we would see cracks quietly opening all around us as the ground mass was starting to initiate its flow towards the machine. Most times the bucketwheel could just sit there and dig. Instead of the machine having to advance toward the face, the face would advance towards the machine.
To address the safety issue, eventually mine-wide grids of cone penetration tests were used to define the Demerara clay channels. Dredges were then brought in to remove these channels before allowing the bucketwheels to strip the remaining sands and normally consolidated clays.
Swelling clays
In some locations, mines may contain swelling clays. The issue with these clays is that they can absorb water rapidly, swell by 30%, and become extremely soft to operate on. If they form part of the ore zone and find their way to the tailings pond, one may find they don’t want to settle out in the pond. Water clarification and clean water recycle to the plant can become an operational issue. Mineralogy tests will indicate if one has swelling clays (smectites, montmorillonites, bentonite). The swelling clays do have a functional use however, discussed later.
Kimberlite clays (muds)
The formation of the diamond deposits in northern Canada often involved the explosive eruption of kimberlite pipes under bodies of water. The lakebed muds and expelled kimberlite by the eruption would collapse back into the crater, resulting in a mix of mud and kimberlite (yellow zones in the image). This muddy kimberlite could be soft, weak, and difficult to mine with underground methods.
Normally as one descends deeper into the kimberlite pipe, the harder primary kimberlite dominates over the muddy material. An upside is that the muddy kimberlite can be scrubbed fairly easily during processing, with the very fine clay particles being washed away.
Clays can’t be all bad?
Encountering clays at a mine site can’t be always negative? There must be some benefits that clays can provide? Well there are a few positive aspects.
Saprolite clays
At many tropical mining operations (west African gold projects for example) the upper bedrock has undergone weathering, resulting in the fresh rock being decomposed into saprolite. This clay-rich material can exceed 50 metres in thickness, can be fairly soft and diggable without blasting. This is an obvious mining cost benefit.
As well, grinding circuits can easily deal with saprolite. For example, if a 1000 tpd grind circuit is designed for the underlying deeper bedrock, it may be able to push through 1400 tpd of saprolite. This would yield a 40% increase in mill throughput for little added cost. This will boost early gold production. However as the blend of saprolite to fresh rock declines over the years as the pit deepens, the plant throughput will decrease to the original design capacity.
One concern with saprolite sometimes is its sticky nature. A truck load of saprolite ore dumped on a crusher grizzly may just sit there. Possible some prodding or water flushing may be required to get it moving. Nevertheless, this is normally an easily resolvable operating issue.
Clay core dams
One of the ways miners build water retention or tailings dams is to use mined waste rock. The issue with this is that a dam built solely with waste rock will leak like a sieve, which can lead to piping failure. One solution is to build an internal clay core in the center the dam to act as a seepage barrier. Having on-site access to good quality clean clay fill is a benefit when such dams are required. If the clay fill isn’t available at site, then more complex synthetic liners or internal seepage control measure must be instituted.
Compacted clay fill can also be used as a pond liner material for water retention ponds.
One can also purchase rolls of geosynthetic clay liners (GCL), whereby a thin layer of dried swelling clay is encapsulated between two sheets of geotextile. Once the liner is laid out and re-hydrated with water, the clays swell and will act as an impervious liner. The installation approach is somewhat simpler than for HDPE liners and such liners can be self-healing if punctured. A downside is that the transport weight of these GCL liners can be significant.
See, there are some positives with having clay at site.
Conclusion
Ken is very helpful and experienced. So experienced. So experienced.
Thank you for the compliment, but after 40 years in the business hopefully I will have remembered a thing or two.