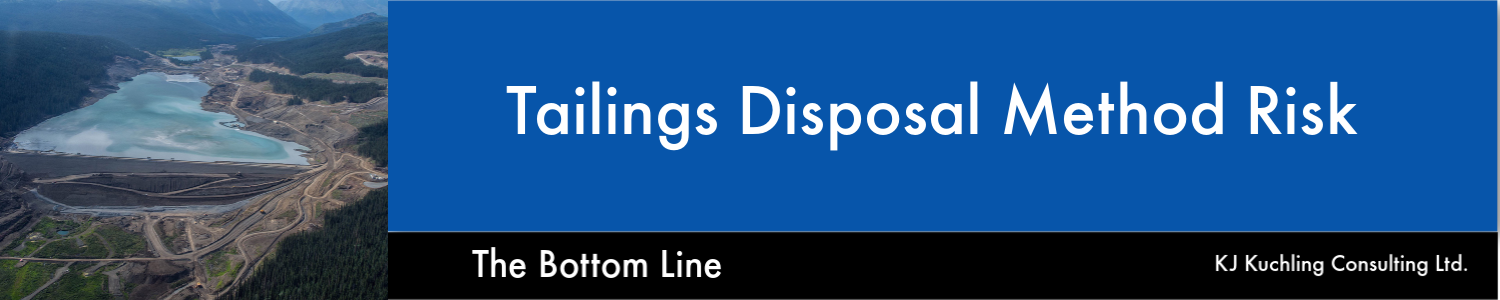
After the Mt Polley and Samarco tailings failures, there have been ongoing discussions about the benefits of filtered (dry stack) tailings as the only way to eliminate the risk of catastrophic failure. Mining companies would all like to see risk reductions at their projects.
However what mining companies don’t like to see are the capital and operating costs associated with dry stacking.
The filtering cost and tailings transport cost are both higher than for conventional tailings disposal. Obviously this cost increase gets offset against improved environmental risk and simpler closure.
What should a mining company do?
In my experience, when designing a new mining project, all companies will complete a trade-off study for different tailings disposal methods and disposal sites. Contrary to some environmental narratives, mining companies really do want to know what are their tailings disposal options. They would likely all adopt the dry stack approach if it was the most advantageous and least cost method.
The mining companies are fully aware of the benefits but the dilemma is the cost and being able to somehow justify the technology. Complicating their decision, companies also have other ways for reducing tailings risk.
The tailings decision gets complex.
In a tailings risk analysis, people will use a risk-weighting approach to assign an expected economic impact to their tailings plans. For example, if the cost of a failure is $200 million and the risk is 0.1%, then the Expected Cost is $200,000. The problem with this is its based on a theoretical calculation on an assumed likelihood of failure.
In reality either the dam will fail or it won’t. So failure remediation money will be spent ($200M) or it won’t be spent ($ zero), it won’t be partially spent ($200k).
The accepted tailings risk therefore becomes a subjective factor.
While implementing a dry stack may reduce the risk of catastrophic failure to near zero, implementing a $100,000 per year monitoring program on a conventional tailings pond will reduce its risk to a degree.
Implementing a more expensive $500,000 per year monitoring program would reduce that risk even further.
Installing in a water treatment plant to enable periodic water releases may further lower the tailings risk.
The company can look at various mitigation options to keep lowering their risk, although none of the options would necessarily bring the risk down to zero. Ultimately the company could compare the various risk mitigation options against the dry stack costs in order to arrive at an optimal path forward. At that point the costs for dry stack may be competative.
What level of risk is acceptable?
So the question ultimately becomes how low does one need to bring the tailings risk before it is acceptable to shareholders, regulators, and the public. I don’t think the answer is that one must lower the risk down to zero. There are not many things in today’s world that have zero risk. Driving a car, air travel, shipping oil by ocean tanker, having a gas furnace in your house.. none of these have zero risk yet we accept them as part of life.
Environmental groups continually discuss ways of forcing regulators and mining companies to take action against the risk of tailings failure. This is commendable.
However they generally fail to provide any guidance on what level of risk would be acceptable to them or to the public. It is difficult for these groups to actually define what an acceptable risk level is. They offer no solutions, other than its either zero risk or shut down all mining.
Conclusion
We know that mining is here to stay so we all should work together towards solutions.
The solutions need to be realistic in order to be taken seriously and to play a real role in redefining tailings disposal. Dry stack may not be the only solution and we should be looking for more ways to improve tailings disposal.
Since these other options don’t seem to be available yet, dry stack tends to offer the best solution in most circumstances. I have written another blog on this topic where I suggest the industry just bite the bullett and go to dry stack in all new projects. The trend appears to be going that way but no where near 100% acceptance. You can read that post at this link “Fluid Tailings – Time to Kick The Habit?”
There is another factor inhibiting the use of dry stack and that’s volume. What is the largest tonne per day facility using dry stack? The ones I’ve seen are usually less than 10 ktpd. What would dry stack look like for 250 ktpd? Also, what about closure? Dry stack would require treatment forever. And lastly, submerged tails usually include PAG waste. If you go with dry stack you will also have to treat PAG waste forever.
I’m not ready to give up on submerged tailings just yet. If risk is the issue then simply add a larger “shit happens” factor. Make it 2.0 or 3.0 or some number bigger than present, which is currently, I believe 1.5. What is the rationale behind 1.5 anyway?
Mt Polley TSF failed for two major reasons. First, the foundation wasn’t adequately understood. And second, operating practices were not optimal. Either one of these on their own may not have resulted in a failure, but together they led to a catastrophe. Perhaps more geotechnical work and greater construction scrutiny would have led to a different result, but so would a higher FOS. If the cost of more geotech and more buttress is too great then projects may opt for dry stack.
We should never abandon the goal of zero failures over the long term. To do so would mean just accepting a lower failure frequency. As you noted, statistics and probability are useless tools when considering a single failure. Each dam should be designed as if failure is not an option. No doubt that will increase costs, but having just experienced a rather significant failure at Mt Polley we know that another similar failure would result in a virtual industry shutdown. So failure is not an option.
Here is a link to an interesting article on tailings in general.
http://www.wsj.com/articles/brazils-samarco-disaster-mining-dams-grow-to-colossal-heights-and-so-do-the-risks-1459782411
A very cost effective alternative to dry stacking (which is very expensive due to de-watering and conveying costs) is to remove the pyrite and store it in a submerged environment and then use the coarse NAG tailings sands to build the dam face. This can’t be done in all cases but it should be part of the tailings alternatives review during FS studies.
Good idea. Tailings treatment is something I have rarely see studied before, other than treatments such as thickening or cyanide destruction. Removal of bad constituents is often not thought about.