Several years ago I did some geotechnical consulting for BHP’s bauxite mining projects along the north coast of Suriname. The mines were located in swampy terrain, underlain by very soft clays. The picture below shows the typical landscape when crossing one of the swamps. Haul roads were needed to access the small satellite bauxite pits, which were spread apart several kilometres. The high ground in the background is one such bauxite deposit.
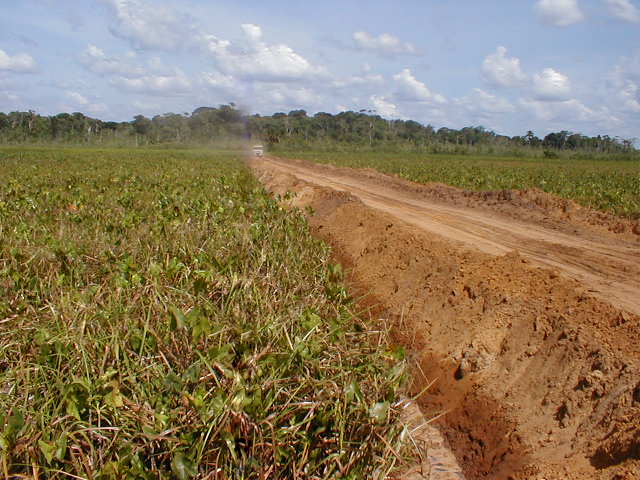
Suriname swamp road for mine
Unfortunately where haul road construction was concerned, there were no nearby gravel pits or road aggregate supplies. However there were significant amounts of fine sand on the high ground “islands” in the swamp. Road building mainly relied on end dumping truck loads of sand, allowing it to settle and sink into the swamp. Then continue adding more and more sand until the settling process stopped. This resulted in high cost roads and very slow progress in construction. Periodic rainfalls, daily during wet season, would cause havoc with the trafficability on the fine sands.
Swamp vegetation to the rescue
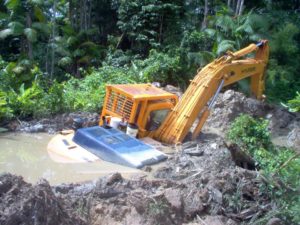
How soft were the swamps clays? See the photo to the right.
Where there was significant swamp vegetation (like in the photo above), it would be buried by the fill, helping to form a mat. This supported the road fill and minimized the sand losses into the sub-grade. However in some parts of the swamp the vegetation was minimal and therefore sand settlement losses could be high.
Geotextiles were applied in some areas, using a geogrid. These were successful although large amounts of sand were still required as the entire road would compress the underlying clay.
Once a road was built, the next issue was the trafficability on the fine sand surface, especially after rains. The sand would rut and require constant grading and repair.
Final road capping would consist of hard laterite when available. Laterite is a high iron off-grade bauxite that could be compacted to form a hard surface but would still degrade and get slippery when wet.
If coarse aggregate had been available locally, road performance would have been much better. However we had to work with what was available.
Geo-cells would have helped
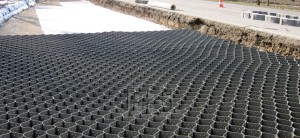
A few years later I saw a video about a geo-cell solution for building roads with sand only. The website is The PRS-Neoweb™ Cellular Confinement System (www.prs-med.com). I think there are other similar geotextiles available but this is one that is well described on their website. Sand is placed into the geoweb, which eventually forms a stiffer layer. I assume that one could place the sand using mobile equipment or by hydraulically pumping coarse sand as a slurry.
In hindsight, I would have liked the opportunity to test the geo-cell system in the swamps of Suriname. Potentially it would have been a good solution to prevent both sand losses and to create a more trafficable surface.
I’m not certain if the best location for the geo-cell would have been along the sub-base of the road to support the sand load or near the surface to help create a more trafficable surface. Maybe it would have been beneficial in both situations.
Building a road over a swamp in Suriname is somewhat similar to building a road out onto a tailings pond. Possibly the geo-cells would have application there too.
Use Hydraulic Sand
Another large earthwork project we undertook in Suriname was building a dragline walkway across a swamp. The walkway was 4 km long, 30 m wide and about 2 m thick. That required a lot of fill. This walkway was built using hydraulic sand. Boskalis, a Dutch dredging company, collect sand from the bottom of the Suriname River, barged it to a staging site about 5 km from the walkway, and then pumped the sand to the construction site.
The hydraulic sand was discharged between two bunds where it quickly settled out. It was somewhat similar to a tailings disposal operation. Placing the sand using this approach was low cost and didn’t require trucks driving out onto the swamp. It also advanced the road with a very shallow front face, avoiding slumping failures or mudwaves ahead of the advance. A few softer sections of the walkway route also incorporated geotextiles.
Engineering teams need to look at options since different procedures may be required when building roads over swamps due to the unstable conditions one may encounter.
Conclusion
Geotextiles have many applications in the mining industry. There can be significant up-front costs to purchase and install them but don’t let that scare you away. The savings may been seen down the line. They are definitely worth a look.
The big issue in Suriname were clays, both under the roads and in the overburden above the bauxite deposits. Clays can have many forms, all of which can be problematic to deal with. I have written another blog post about my experiences with the different types of clay and how they may behave. If interested, check it out at “Clays and Mining – Friends or Foes?“
Note: You can sign up for the KJK mailing list to get notified when new blogs are posted. Follow me on Twitter at @KJKLtd for updates and other mining posts.
The benefits of well designed, constructed and maintained roads are underestimated by many managers nowadays. It’s hard to spend money to crush proper road dressing when metal prices are collapsing but it’s money well spent to increase tire life and reduce rolling resistance.
A company in Poland has sent me their web link whereby they also distribute geocells.(www.geoglobe.pl)
Project managers, landscape companies, and engineers from around the globe have used BaseCore geocells. Real-world commercial projects rely on HDPE, military-strong products that last