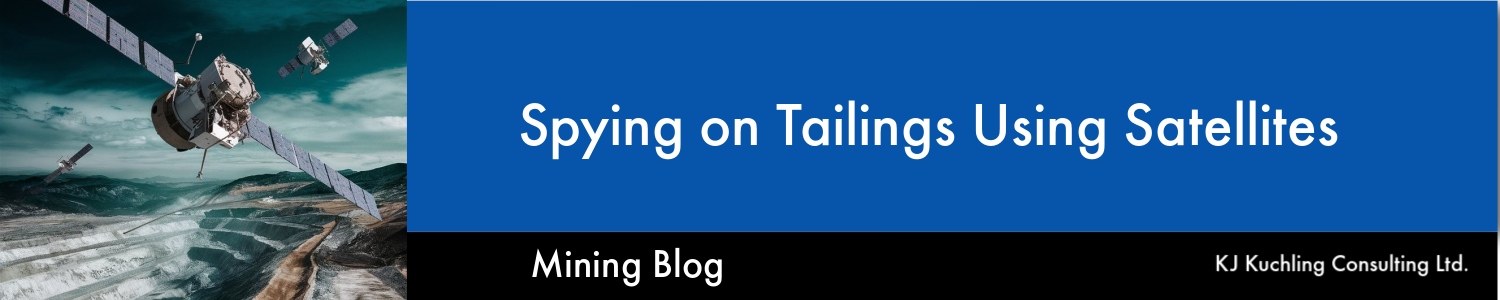
There have been recent heap leach pad failures in the Yukon and Turkey and tailings dam failures in Chile and the Philippines. As a result I have been seeing more posts on LinkedIn about the application of satellite based InSAR deformation monitoring. Prior to that I had never heard of InSAR, so thought a little bit of background study might be worthwhile.
The following are my observations on what InSAR is and where it may be going. I am by no means an expert in this technology. I am merely viewing it from the perspective of a mine design engineer.
What is InSAR
InSAR is satellite-based “Interferometric Synthetic Aperture Radar”. It can measure the distance from a satellite to a ground feature. With repeated imaging it is used to detect changes in distance and measure displacements to within 5-10 millimetre accuracy. Hence it can be used as a potentially cost-effective slope monitoring tool, albeit it cannot be the only tool, as discussed later.
The relevant satellite images have been available for years. Currently the availability of analytical software to interpret the satellite data is improving. It can detect millimeter-scale displacements, however only in the line-of-sight (LOS) direction of the satellite. Using two or more satellites in different orbits, displacements in horizontal and vertical directions can be defined.
An example of a satellite being used is the Sentinel-1, launched in mid-2015 by the European Space Agency. This satellite information is open-source data. It will have a 6 to 12 day revisit cycle in many locations.
The results of an InSAR displacement survey are typically shown as a series of colored data points, typically coloured green for the stable points, trending to yellow and red for points that are moving.
This blog has some example images.
Some Limitations With InSAR
There are some limitations with InSAR, so it can only be part of a monitoring program. These limitations are:
-
The displacement direction is only measured in the direction of the satellite. Hence one may not know in which direction the movement is occurring. The magnitude of displacement could be underestimated depending on the apparent angle of measurement.
-
The movement being measured could consist of vertical settlement due to material consolidation and may not be horizontal and related to impending failure.
-
The displacement magnitude measured on opposite sides of a facility may have different accuracy, depending on the slope orientation versus the line-of-sight.
-
Areas with heavy vegetation may be difficult to monitor
-
Areas with heavy or persistent cloud cover can be difficult to monitor.
-
Areas with snow cover will be difficult to monitor.
-
The satellite return period may be weekly or every two weeks, so one is not able to analyze daily movements if a situation is critical. If the return visit day has cloud cover, there will be no new satellite data collected.
-
Areas with on-going construction or tailings deposition will lead to erroneous results.
-
Due to the line of sight, not all slope failure modes may be detectible (for example piping failure).
Regardless of these limitations, InSAR can still play a role in any monitoring program since it is able to monitor large areas quickly. Consider it as a pre-screening tool, being aware that not all failure modes may be detectible with it.
Discussion
On LinkedIn, one can see numerous posts where independent experts are examining historical InSAR data for recent failures to see whether early movement should have been detected. The results seem to be quite positive in that areas that have failed might have been red-flagged prior to failure.
There are also zones that showed critical displacements but have not failed.
Typically, there are four ways to monitor displacement in pit slopes, tailings dams, heap leach pads, and waste dumps. They are:
-
Insitu monitoring using embedded instruments, for example slope indicators, extensometers, and settlement gauges. These instruments provide information on what is happening internally within a slope, where actual movement is occurring, and they can be used in warning alert systems.
-
Surface monitoring using radar (ground based InSAR) systems and survey prisms. These tools measure only surface movements in selected areas, can be monitored as frequently as needed on an automated basis, and integrated into warning alert systems.
-
Drone or aerial surveys can be used to measure topography and monitor movements over large areas. This method requires a data processing delay (not real time) to derive the movement information, but such surveys can be done as frequently as needed.
-
InSAR from satellite can be used over very large regions to highlight areas with movement. That should trigger the implementation of one or more of the other monitoring approaches (if not already in place).
Conclusion