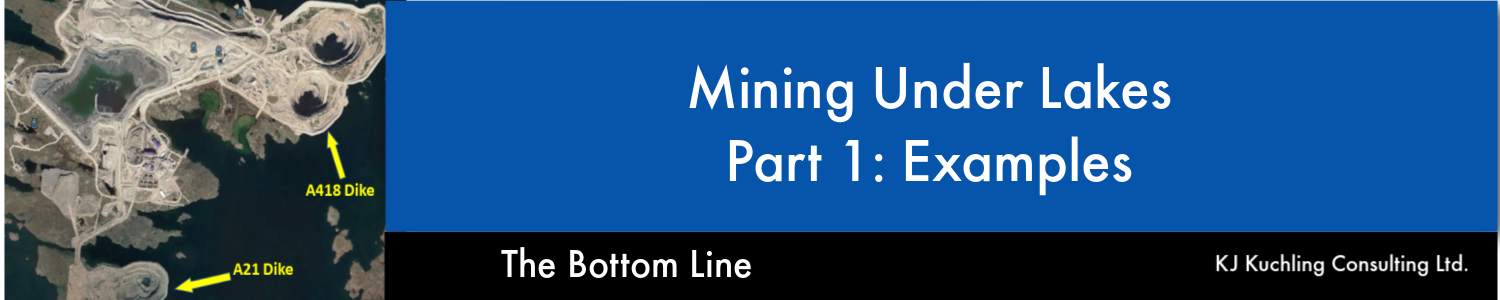

Springpole Project
I recently saw an investor presentation from First Mining Gold about their Springpole Project. The situation is that their open pit is located within a lake and will require the construction of a couple of small cofferdams to isolate the pit area from the lake. The concept is shown in this image.
Over the last couple of years I have been involved in a few early-stage studies for mining projects in which nearby bodies of water play a role in the design. In Canada’s north there are thousands of lakes and rivers, so its not surprising to find mines next to them.
That got me thinking about how many other mines are in the same situation, i.e. projects that may be located very close to, or within, a lake, river, or ocean. Hence I have compiled a short list of a few such mines.
I have been directly involved with some of those in the list, while others are only known to me with limited detail. Some mines I had never heard of before, but their names were provided to me by some Twitter colleagues.
My observation is that building a mine within, or adjacent to, a body of water is nothing new and this has been done multiple times successfully.
Some of these projects may refer to the dams as “dikes”, “cofferdams”, “sea walls” but I assume they are all providing roughly the same function of holding back water for the life of the project. They are not viewed as permanent dams.
This is Part 1 of a two-part blog post. Part 1 provides some examples of projects where water bodies were involved in the design. Part 2 provides a discussion on specific geotechnical and hydrogeological issues that would normally have to be examined with such projects.
Some Lake Mining Examples
The following are some examples of operating mines involving lakes. I have captured a few Google Earth images, unfortunately some have only low resolution vintage satellite imagery.
Diavik Diamond Mines, NWT
This is a project I was working on with in 1997 to 2000 while it was still at the design and permitting stage. My role focused on pit hydrogeology and geotechnical as well as mine planning.
The project would require the construction of three dikes in sequence to mine four lakebed kimberlite pipes.
The three dikes were named after the associated kimberlite pipe being mined inside it; A154, A418, and A21.
The first dikes were built in 2002 and the last dike (A21) was completed in 2018.
The total dike length for the three dikes is about 6.2 km.
For those interested in learning a bit more about Diavik, I have posted an earlier article about the open pit hydrogeology there, linked to at " Hydrogeology At Diavik – Its Complicated".
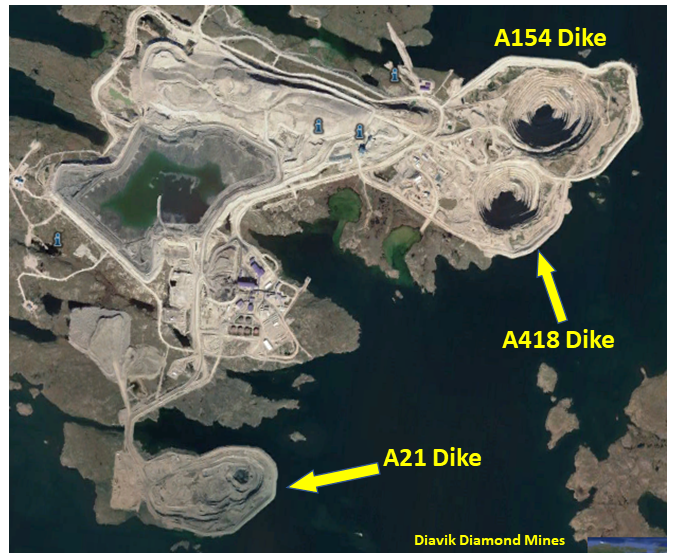
Gahcho Kue, NWT
This is a DeBeers diamond project was built in 2016 and required the construction of several small dikes to allow access for open pit mining. The photos show the pre-mining situation and the site as it is today. One can see the role the lake would play in the site layout and the need for multiple small dikes.
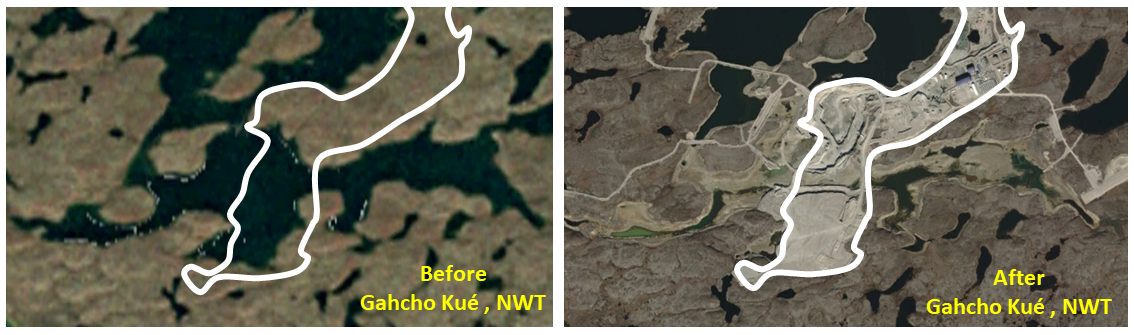
Meadowbank, NWT
This is an Agnico-Eagle gold mining operation built in 2010 that required a cofferdam to be built around one of their open pits (see image).
The total dike length is about 2000 metres. I don't know much more about it than that unfortunately.

Cowal Gold Mine, Australia
Yes, a lake in Australia ! This is a former Barrick operation, now owned by Evolution Mining, and is another example where the mine is located within the shoreline of a lake (Lake Cowal). I don't know much about this, the name was kindly provided to me by a colleague.
The total dike length appears to be about 3000 metres.
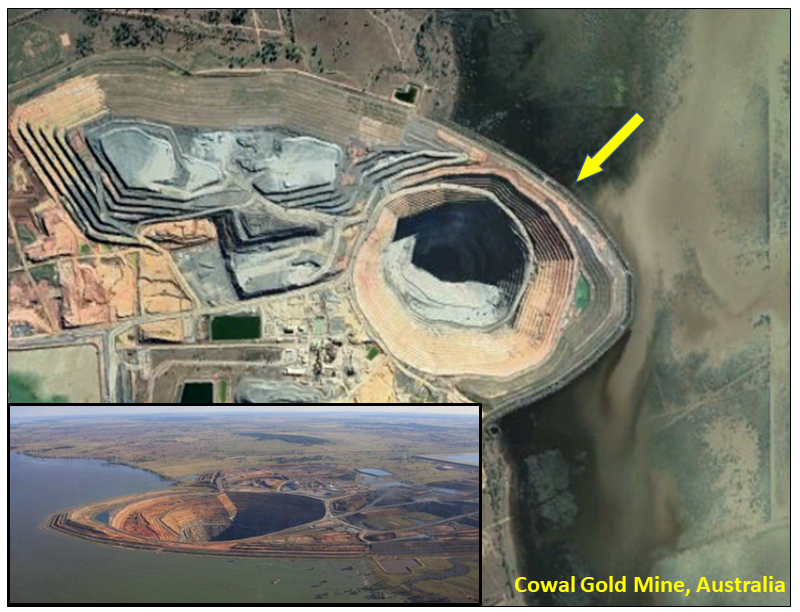
Rabbit Lake Sask
The historical Rabbit Lake uranium mining operation required the construction of cofferdams around a few of their open pits. They are now reclaimed and flooded.
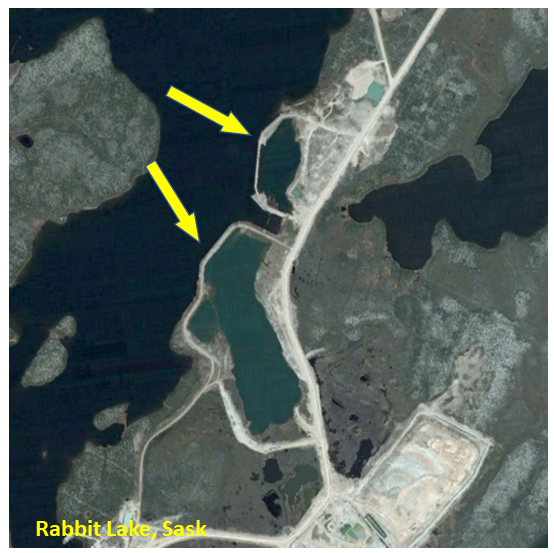
St Ives Gold Mine, Australia
This is a unique situation in that several pits are located within an ephemeral (intermittent) salt lake and dikes were required to prevent pit flooding during wet season.
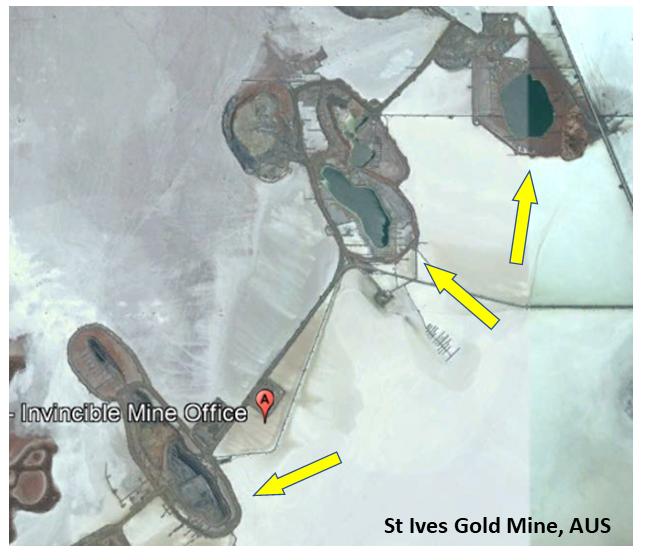
Some River Mining Examples
The following are some examples of operating mines involving rivers. Rivers provide a somewhat different design challenge since they have flowing water, who's volume and velocity may change seasonally. Constrictions in the river created by the dike itself may increase the flow velocity and erosion potential.
Gorevsky Mine, Siberia
This lead-zinc operation has an orebody that extends into the Angara River.
This mine has built a fairly large cofferdam into the river, and is currently mining a large pit within it. The total cofferdam length appears to be about 4000 metres.
It would be interesting to see how close the pit will get to the cofferdam. We'll check back in a few years.
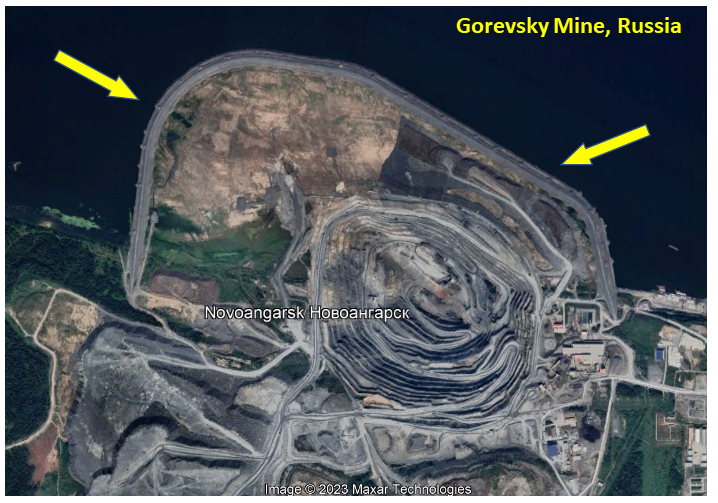
BHP Suriname Bauxite Mine
This is a project I was involved with several years ago. The bauxite deposit extends beneath the Suriname River and the goal was to mine as much ore as possible.
Given the flow rates in the river, especially during the wet season, it would be difficult to maintain a cofferdam out into the river.
The shoreline overburden consisted of sands and soft clays, so the decision as made to construct a sheet piling wall along the river bank to protect the pit from river erosion. This was mined out successfully and eventually reclaimed.

McArthur River, Australia
In situations where the river (creek) is small enough and the topography allows, one can divert the entire river around the mine.
There are several examples of this in Canada and elsewhere. Here’s the McArthur River lead-zinc mine in Australia, where they channeled their small river around the open pit.

An Ocean Example
There are some examples of mining near the ocean. These operations may need to deal with large storm water level surges and large tidal fluctuations. The Island Copper Mine on northern Vancouver Island is an example where they mined close to the shoreline but not actually into the ocean (as far as I am aware).
Cockatoo Island Mine, Australia
This interesting iron ore mine has an ore zone that dips 60 degrees, is 35 metres wide, with a strike length of more than one kilometre.
A sea wall was constructed to prevent any tidal water from entering the open pit that was to be mined, with reportedly high tidal fluctuations there.
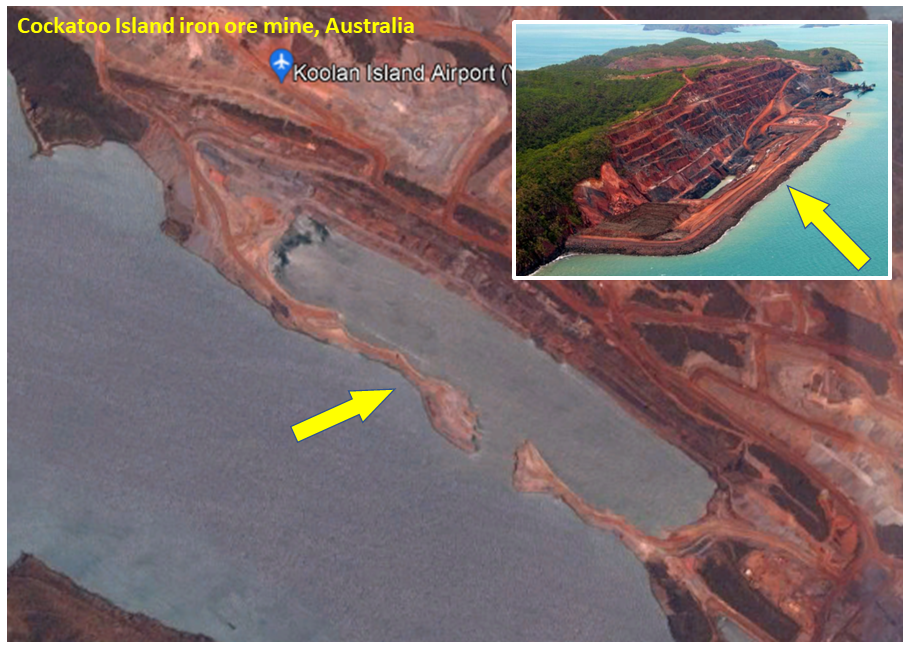
Conclusion
As one can see, the idea of mining into a body of water is nothing new. Its not a preferred situation, but it can be done economically and safely. The technical challenges are straightforward, and engineers have dealt with them before. However there also are instances where the design could not economically address the water issue, and thus played a role in the mine not getting built.
If you know of other mines not listed above that have successfully dealt with a water body, please let me know and I can update this blog post.
This concludes Part 1. Part 2 can be read at this link " Mining Under Lakes – Part 2: Design Issues" discusses some of the concerns that engineers need to consider when building a mine in these situations.
Pantai Remis tin mine
Finally, the worst-case scenario is shown in this grainy video of a tin mine (Pantai Remis Mine) pit slope failure. It seems they mined too close to the ocean. Watch to the end, its hard to believe. Its looks like something out of a Hollywood disaster movie.