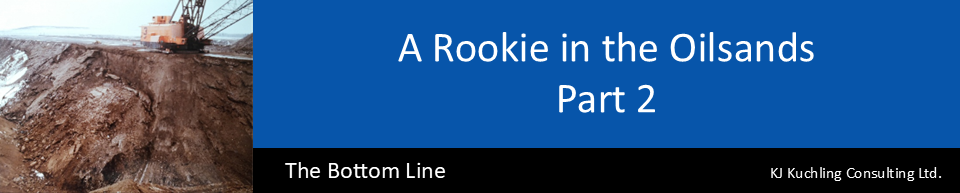
The article is Part 2 of discussion on my experiences working in the oilsands at the Syncrude Mine in northern Alberta. Part 1 can be read at this link https://kuchling.com/a-rookie-in-the-oilsands-part-1/
In Part 1, I described the great Engineer-in-Training rotational program that Syncrude had in place for new engineering graduates. Initially I had rotated through the Overburden Geotechnical and Industrial Engineering departments. I was then fortunate enough to go though the Mine Geotechnical department and Short Range Planning. Here are some experiences from those assignments.
Will the Draglines Be Safe
Syncrude had four large walking draglines, each with a 80 cubic metre bucket and 110 metre operating radius. These were very big machines; you could sit one in the end zone of a football field and the bucket would be digging (or dumping) in the other end zone. Two draglines were on the East side of the mine and two were on the West, mining the oilsand in 25 m wide strips.
Mining oilsand while from the top of a 50 metre high and 45 degree highwall had never been done before. The geotechnical conditions were new. They were also dramatically different on the East and West sides of the mine, even though mining in the same orebody.
The East side was far more a greater geotechnical concern than the West side. I happened to be the West side mine geotechnical engineer (lucky for me I guess).
The oil sands are sedimentary deposits, and consist of inter-layered sands, silts and clays. At the Syncrude mine, the clay layers were regionally dipping towards the west at 5 to 10 degrees (as shown in the sketch below). Hence they were dipping into the wall on the West side and dipping out of the wall on the East side. The orebody also contained ancient creek scour channels, now infilled with clays and sands.
On the flanks of these scour zones, the thin clay layers could dip up to 25 degrees out of the wall. This was a problem. In university we learned rock slope failures generally require 30-35 deg dipping joint structures for sliding to occur; but here in the clays, sliding (block slides) could occur along 15 to 25 deg dips.
There were numerous instances of East mine block slides, where large portions of the upper slope would fail as large blocks, 50 metres long and up to 30 metres back from the crest. The fear was that if a dragline happened to be sitting on one of these failing blocks, the entire machine would slide along into the pit. Many block slides did occur over the years, but only a few came close to jeopardizing a machine. The geotechnical monitoring programs in place were successful (described later).
The insitu clay structures were identified using oil and gas borehole logging technology, with tadpole dipmeter plots (see image) used to analyse the bedding (the tail on the tadpole shows the dip direction). The vertical axis is depth from surface or elevation. The geotech engineers would use this information, combined with structural mapping of previously mined faces, to forecast potentially unstable areas.
In these problem areas, the geotech teams would install slope indicators that were monitored while the dragline was mining through the area. Dedicated 24 hour field engineers were assigned to each of the East side draglines and mining operations were closely monitored at all times.
It was not uncommon for the Syncrude geotechnical engineer to get a 2 am phone call at home saying movement has been detected and they walked the dragline back from the face and then get asked “What should we do now?”.
In the places that the engineers knew were going to be very risk, they could implement mitigation measures. How would you deal with the steeper scour zones? They had three main options.
-
mine through the area with intense geotechnical monitoring in place, using slope indicators, survey prisms, and visual ground inspections.
-
sub-excavate the zone; using the dragline to dig out the area and then backfill with the same material to destroy the clay bedding. Then they could safely mine through the area, although the days used to sub-excavate would remove the dragline from oilsand production.
-
another option was to blast the area ahead of time, to destroy the clay bedding and allow pore pressure dissipation.
All three options were available at the discretion of the geotechnical engineering team. However they all cost money and/or loss in mining production, but safety was always the priority.
The four draglines are now mothballed and thankfully none were ever harmed. All oilsand mining operations are now based on truck-shovel systems.
Basal Slope Failures
On the West side of the mine, the bedding was mainly into the highwall, so block slides were not a major concern. In my brief time there, we never had a block slide on the West side although we did continually review dipmeter plots and face mapping results. One still couldn’t be too careful or get lazy.
The main geotechnical issue on the West side were basal slope failures, termed this due to sliding along weak clays and muds at the base of the highwall. This photo shows a typical basal failure. Basal failures also occured on the East side.
Generally, these slope failures did not jeopardize the dragline since they occurred on freshly cut highwalls away from the machine. Eventually the dragline would be required to operate next to existing basal failures when mining the next panel (as shown in the photo).
The dragline would sit 15-25 metres from the wall, the closer is better to maximize reach into the pit.
The main concern with basal failures was that the toe of the failed slope would move beyond the reach of the dragline and could not be mined. As well, sometimes the dragline would need to cast waste layers back into the mined out pit while avoiding the burial of the oilsand toe. If the waste couldn’t be cast back inpit due to toe failure, it would be placed on the operating bench and trucked away later (at a cost).
The Alberta government focused on maximizing oilsand resource recovery. If the dragline could not reach the ore due to a failure, we would need to send mobile equipment down to get it. If we couldn’t do this due to access issues, we needed to prepare an Ore Loss Report that was tracked and submitted to the government agency (ERCB). We hated to submit those reports, taking it as a personal disappointment that we couldn’t get to that ore.
In the basal failure photo, one can see a vertical scarp next to the dragline. The oilsands were a “locked sand” in that the sand grains were tightly compacted or interlocked from the compressive weight of over a kilometre of glacial ice thickness in the past. The vertical scarps would stand indefinitely, sometime spalling off in slabs. The oilsand itself was a very strong geotechnical unit (friction angles in excess of 50 degrees).
Conclusion