In my view one thing lacking in the mining industry today is a consistent approach to quantifying and presenting the risks associated with mining projects. In a blog written in 2015 titled “Mining Cashflow Sensitivity Analyses – Be Careful” I discussed the limitations of the standard “spider graph” sensitivity analysis often seen in Section 22 of 43-101 reports.
This blog post expands on that discussion by describing a better approach. A six-year time gap between the two articles – no need to rush I guess.
This blog summarizes excerpts from an article written by a colleague that specializes in probabilistic financial analysis. That article is a result of conversations we had about the current methods of addressing risk in mining. The full article can be found at this link, however selected excerpts and graphs have been reprinted here with permission from the author.
The author is Lachlan Hughson, the Founder of 4-D Resources Advisory LLC. He has a 30-year career in the mining/metals and oil gas industry as an investment banker and a corporate executive. His website is here 4-D Resources Advisory LLC.
Excerpts from the article
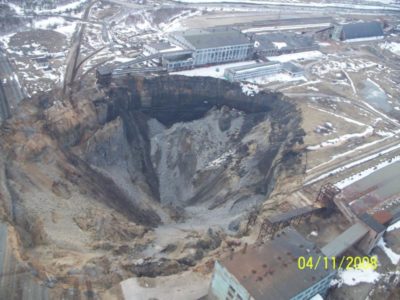
Mining can be risky
“The natural resources industry, especially the finance function, tends to use a static, or single data estimate, approach to its planning, valuation and M&A models. This often fails to capture the dynamic interrelationships between the strategic, operational and financial variables of the business, especially commodity price volatility, over time.”
“A comprehensive financial model should correctly reflect the dynamic interplay of these fundamental variables over the company life and commodity price cycles. This requires enhancing the quality of key input variables and quantitatively defining how they interrelate and change depending on the strategy, operational focus and capital structure utilized by the company.”
“Given these critical limitations, a static modeling approach fundamentally reduces the decision making power of the results generated leading to unbalanced views as to the actual probabilities associated with expected outcomes. Equally, it creates an over-confident belief as to outcomes and eliminates the potential optionality of different courses of action as real options cannot be fully evaluated.”
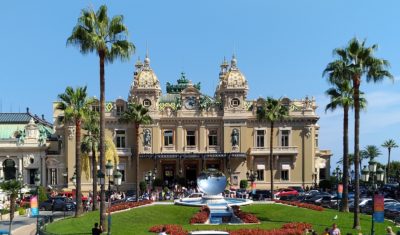
Monte Carlo can be risky
“Fortunately, there is another financial modeling method – using Monte Carlo simulation – which generates more meaningful output data to enhance the company’s decision making process.”
Monte Carlo simulation is not new. For example @RISK has been available as an easy to use Excel add-in for decades. Crystal Ball does much the same thing.
“Dynamic, or probabilistic, modeling allows for far greater flexibility of input variables and their correlation, so they better reflect the operating reality, while generating an output which provides more insight than single data estimates of the output variable.”
“The dynamic approach gives the user an understanding of the likely output range (presented as a normal distribution here) and the probabilities associated with a particular output value. The static approach is relatively “random” as it is based on input assumptions that are often subject to biases and a poor understanding of their potential range vs. reality (i.e. +/- 10%, 20% vs. historical or projected data range).”
“In the case of a dynamic model, there is less scope for the biases (compensation, optionality, historic perspective, desire for optimal transaction outcome) that often impact the static, single data estimates modeling process. Additionally, it imposes a fiscal discipline on management as there is less scope to manipulate input data for desired outcomes (i.e. strategic misrepresentation), especially where strong correlations to historical data exist.”
“It encourages management to consider the likely range of outcomes, and probabilities and options, rather than being bound to/driven by achieving a specific outcome with no known probability. Equally, it introduces an “option” mindset to recognize and value real options as a key way to maintain/enhance company momentum over time.”

Image from the 4-D Resources article
“In the simple example (to the right), the financial model was more real-world through using input variables and correlation assumptions that reflect historical and projected reality rather than single data estimates that tend towards the most expected value.”
“Additionally, the output data provide greater insight into the variability of outcomes than the static model Downside, Base and Upside cases’ single data estimates did.”
The tornado diagram, shown below the histogram, essentially is another representation of the spider diagram information. ie.e which factors have the biggest impact.
“The dynamic data also facilitated the real option value of the asset in a manner a static model cannot. And the model took less time to build, with less internal relationships to create to make the output trustworthy, given input variables and correlation were set using the @RISK software options. This dynamic modeling approach can be used for all types of financial models.”
To read the full article, follow this link.
Conclusion
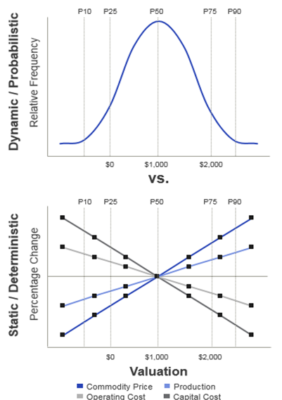
image from 4-D Resources article
Improvements are needed in the way risks are evaluated and explained to mining stakeholders. Improvements are required given increasing complexity in the risks impacting on decision making.
The probabilistic risk evaluation approach described above isn’t new and isn’t that complicated. In fact, it can be very intuitive when undertaken properly.
Probabilistic risk analysis isn’t something that should only be done within the inner sanctums of large mining companies. The approach should filter down to all mining studies and 43-101 reports.
It should ultimately become a best practice or standard part of all mining project economic analyses. The more often the approach is applied, the sooner people will become familiar (and comfortable) with it.
Mining projects can be risky, as demonstrated by the numerous ventures that have derailed. Yet recognition of this risk never seems to be brought to light beforehand.
Essentially all mining projects look the same to outsiders from a risk perspective, when in reality they are not. The mining industry should try to get better in explaining this.
Management understandably have a difficult task in making go/no-go decisions. Financial institutions have similar dilemmas when deciding on whether or not to finance a project. You can read that blog post at this link “Flawed Mining Projects – No Such Thing as Perfection“
Note: You can sign up for the KJK mailing list to get notified when new blogs are posted. Follow me on Twitter at @KJKLtd for updates.